The HDPE Recycling
HDPE - The Base Plastic
High-Density Polyethylene (HDPE) represents a massive portion of global plastic production, estimated at nearly 30%. Yet, here in Canada, the recycling reality is stark: reports indicate only about 9% of all plastic waste is actually recycled. This significant gap means vast quantities of used HDPE – a versatile and durable material – end up in landfills or the environment. This situation highlights a largely untapped resource that is both cheap and readily available, presenting a compelling case for developing innovative recycling solutions.
The Initial Idea
Seeing vast amounts of HDPE ending up in landfills, potentially harming our ecosystems, posed a direct question: couldn't this perceived waste be transformed into something valuable? The breakthrough came during early experiments. A sample combining HDPE with just 3% Kevlar pulp unexpectedly demonstrated the ability to stop ballistic threats. This pivotal result sparked a crucial thought: if even this basic composite showed promise, could waste HDPE itself, perhaps processed in novel ways, be turned into affordable, life-saving protective materials? This idea became the driving force for further research
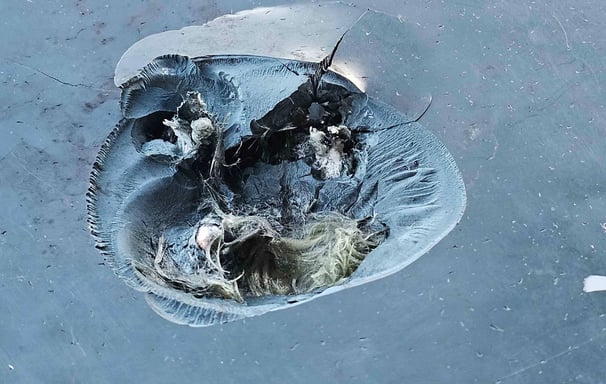
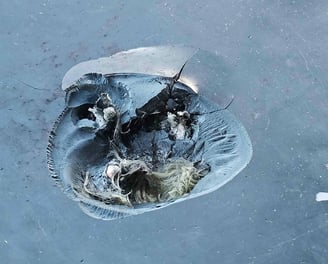
First serious prototype
Moving from the initial concept, the first tangible prototype involved creating a composite matrix using PLA (Polylactic Acid) and waste Kevlar pulp. A key goal here was exploring methods to utilize the Kevlar waste, known for its environmental persistence. This experiment successfully demonstrated the feasibility of impregnating Kevlar fibers with a thermoplastic matrix. Despite this proof-of-concept, the prototype itself had limitations: the sample was bulky, and the impregnation wasn't uniform or complete. This outcome, while not yielding a usable product, was a critical learning phase, confirming the impregnation potential while clearly defining the process challenges (like achieving better saturation and density) that needed to be addressed in subsequent iterations.
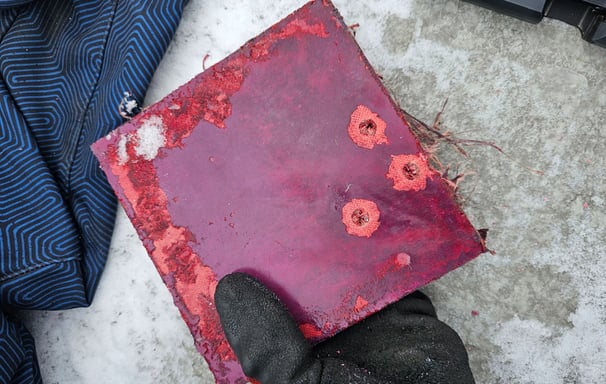
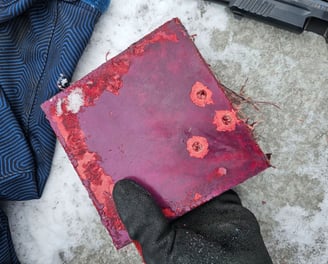
First serious prototype
Significantly, the sample stopped the first 9x19mm impact – a major step confirming potential. Yet, it failed upon the second impact, exhibiting delamination and shattering of the brittle PLA. This outcome, showing both initial promise and clear failure points (poor bonding, matrix inadequacy), was a critical learning phase. It validated the core idea while pinpointing the exact process and material challenges (better saturation, tougher matrix) to overcome. It was from this foundational, albeit flawed, result that the idea truly blossomed.
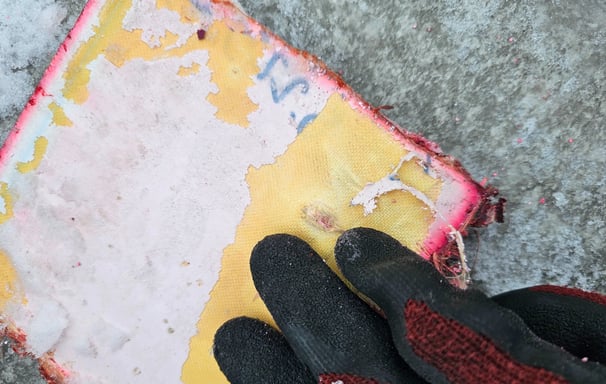
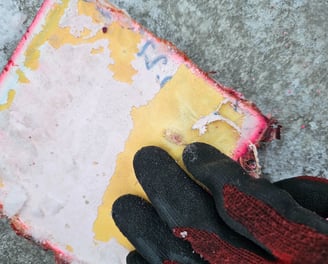
Delamination Failure Testing
Following the significant delamination observed in our initial PLA/Kevlar prototype after the second impact, the immediate next step was to specifically address layer bonding and multi-hit resistance. To investigate this, a new, thin sample utilizing HDPE as the matrix material was manufactured and subjected to a rigorous testing protocol involving a significant number of repeated ballistic impacts. Crucially, this testing revealed that the HDPE-based sample was substantially more resistant to delamination failure compared to the previous PLA composite. This finding validated HDPE's superior performance in maintaining integrity under multiple stresses and confirmed its suitability as the primary matrix material moving forward.
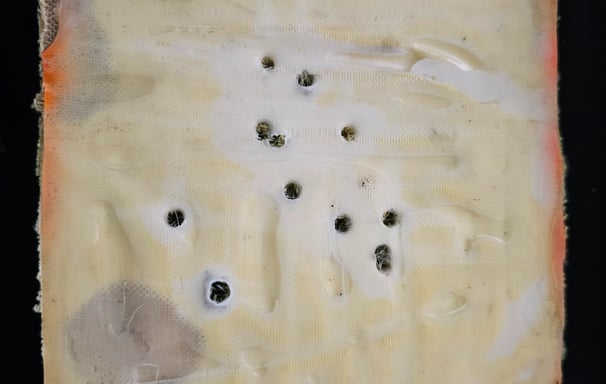
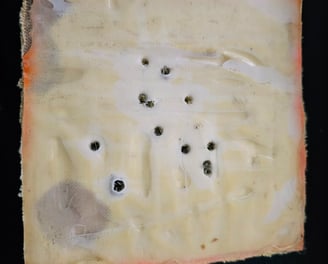
Backside of the Delamination failure
The earlier testing phase pinpointed the path forward. Through targeted improvements in our production methodology and the confirmed benefits of using an HDPE matrix, delamination ceased to be the primary failure mode observed under multi-hit testing. This successful combination of material science and process engineering effectively addressed the critical weakness identified in initial prototypes.
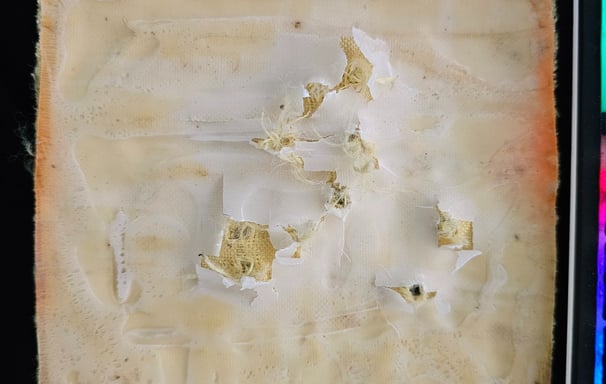
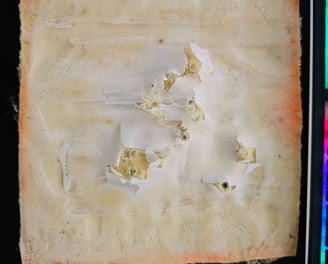
Tensile Testing
While seeing the material stop bullets in field testing was exciting, quantifying its actual mechanical properties was the critical next step. This led to an unexpected but revealing challenge during tensile testing at the UBCO School of Engineering. Our initial attempts using the standard equipment in the Mechanical Engineering lab proved insufficient – we actually managed to overload the machine! Consequently, we had to coordinate with the Civil Engineering department to utilize their higher-capacity tensile tester, capable of handling the forces needed to accurately measure the material's impressive strength.
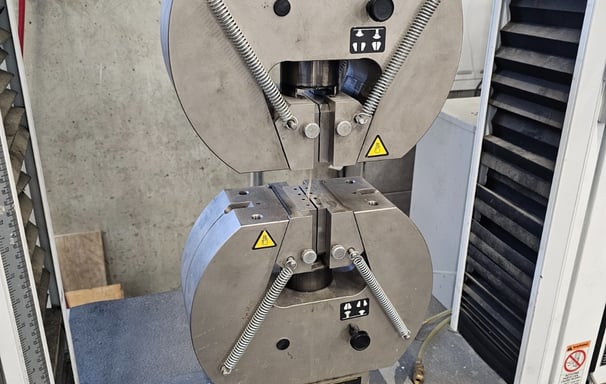
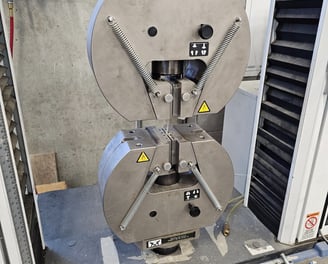
Tensile Testing
Tensile tests were performed according to standard procedures to determine the ultimate strength of the developed material composition. The results indicated a robust mechanical performance, with the material yielding an average tensile strength greater than 400 MPa. (Calculated from an average peak load of 1.5 kN during testing). This significant tensile strength highlights the effectiveness of the approach in creating a strong, resilient material from the constituent components.
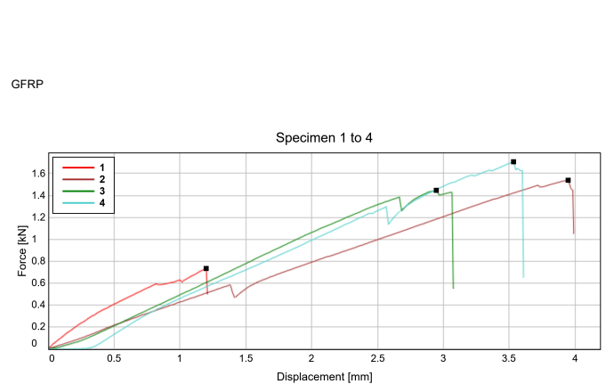
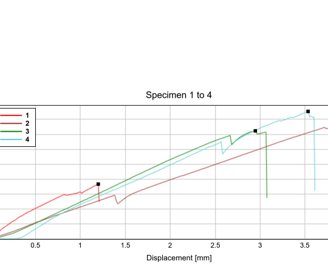
Further Testing
More coming soon
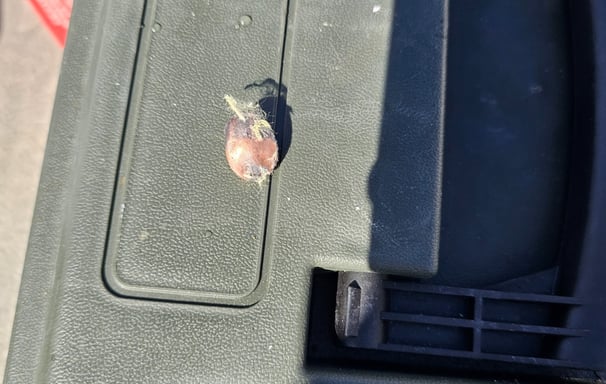
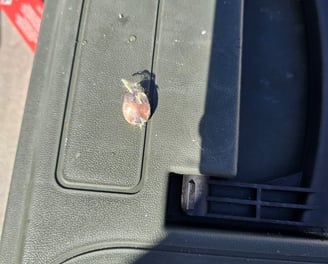