My professional works
BD Screamer HE300VG RAM 3500 Gen 5
This project involved the ground-up design and development of an aftermarket performance turbocharger specifically engineered for the Gen 5 Cummins 6.7L diesel engine, commonly found in Ram Heavy Duty trucks.
Challenge: The primary goal was to significantly increase airflow potential compared to the OEM turbocharger, enabling substantial horsepower gains, while critically maintaining compliance with stringent California Air Resources Board (CARB) emissions standards – a significant engineering challenge requiring careful balance between performance and emissions control.
Solution & Role: My responsibilities centered on the mechanical design of the turbocharger. This included optimizing the aerodynamic profiles of the compressor and turbine wheels, designing efficient flow paths within the housings, and selecting appropriate materials and bearing systems to handle increased loads and rotational speeds. A key focus was integrating design features necessary to meet performance targets without compromising emissions compliance required for CARB certification.
Results: The resulting turbocharger design demonstrated the capability of nearly doubling the stock horsepower output (when paired with appropriate engine tuning and supporting modifications). Crucially, this significant performance increase was achieved while successfully securing CARB certification, making it a street-legal upgrade even in emissions-restricted areas.
CARB EO No. D-553-14
SEMA Certification No. Sc-BDD01-0018
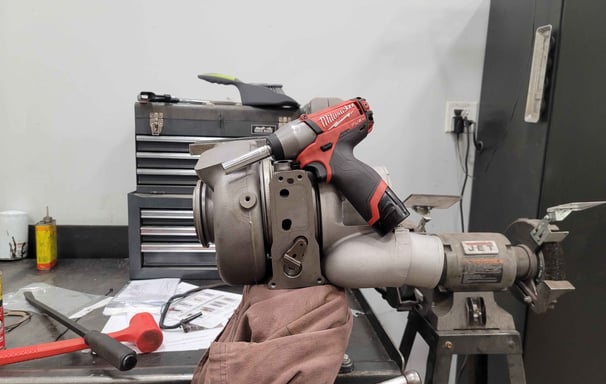
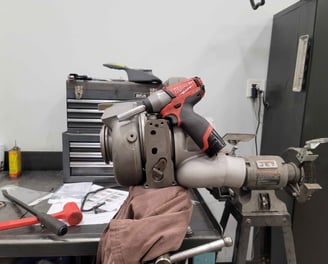
An injector line set that actually fits
Problem: A common frustration in the diesel aftermarket is the poor fitment of many replacement fuel injector lines. Often manufactured with inadequate tolerances ("made in the same cheap factory"), these lines frequently require bending or modification by the end-user, risking leaks, improper seating, and installation difficulties.
Solution: To address this prevalent issue, this project focused on developing a line of diesel fuel injector lines engineered for a guaranteed, direct fit. By adhering strictly to OEM specifications for geometry, material, and manufacturing tolerances, these lines were designed to install directly into the injector pocket without any user modification – just like the original equipment.
Benefits: This approach ensures proper sealing, reliable fuel delivery, and significantly simplifies the installation process, saving time and preventing potential damage often associated with forcing or modifying ill-fitting components.
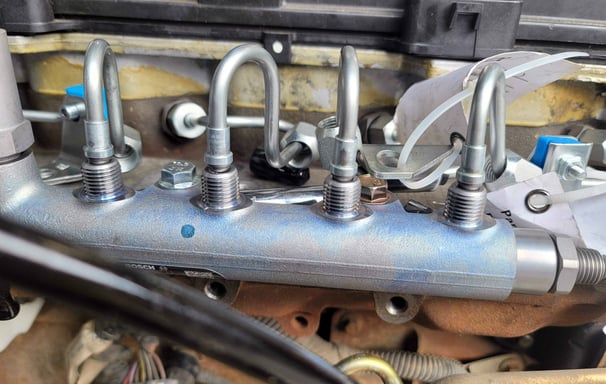
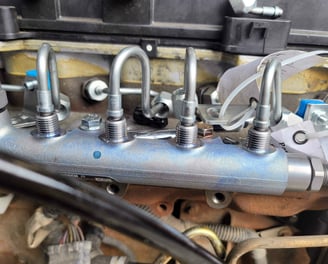
Bosch Lidar Sensor Development - SPAD Detector
Context: Contributed to the development of next-generation automotive LiDAR systems at Bosch, a critical technology for autonomous driving and advanced driver-assistance systems (ADAS). This project focused on optimizing Single Photon Avalanche Diode (SPAD) detectors, a core component enabling high-resolution Lidar.
Challenge: The LiDAR industry faced a persistent and costly challenge related to the calibration of SPAD detectors during production, impacting manufacturing yield, sensor performance, and overall system cost.
Contributions & Impact:
Designed a Novel Production Process: Conceptualized and designed an innovative production process specifically for SPAD detectors. This breakthrough directly addressed and solved the long-standing calibration bottleneck that had previously plagued the industry.
Massive Cost Savings: The new calibration methodology enabled by this process is estimated to save the automotive sector nearly €600 million annually, significantly reducing the cost barrier for advanced Lidar deployment.
Developed Custom Hardware Drivers: Created specialized hardware drivers using SCPI, Python, and MATLAB to interface with and control highly experimental electro-optical sensors used during development and testing.
Constructed Precision Test Bench: Built a specialized V&V test bench capable of achieving repetitive mechanical positioning accuracy in the micrometer range, facilitating comprehensive and reliable characterization of SPAD detector performance.
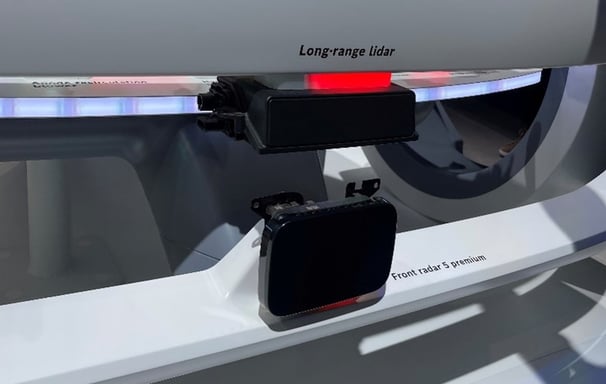
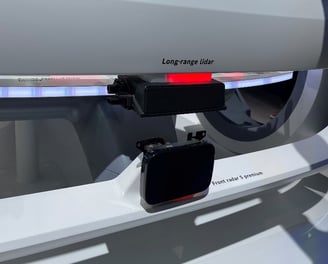
Edmonton Fire Service frame separation
Context: City of Edmonton's Fire Rescue Service operates specialized, extreme-duty vehicles essential for public safety. These assets face exceptional environmental stresses from harsh weather and demanding operational tempos, impacting their durability and service life. Strategies for rapid repair and life extension are crucial for maintaining fleet readiness and managing costs.
Challenge: A key aspect of managing such a fleet involves addressing wear, potential failures, and ensuring vehicles consistently meet safety standards. This project involved certifying specific EFRS vehicles that had been identified as unsafe, requiring a thorough technical evaluation within the broader context of maintaining a resilient and long-lasting fleet.
My Contribution: My work focused on the safety certification of these critical vehicles. This process involved detailed inspection, analysis of failure modes potentially exacerbated by environmental factors, and verification against safety regulations. This hands-on assessment provided valuable insights into the real-world effects of extreme operational stress, informing the certification decision and contributing to the understanding needed for developing better repair and preventative maintenance strategies aimed at extending service life.
Outcome: Successfully completed the required safety certifications, enabling critical EFRS vehicles to return to service. The technical findings supported the broader objectives of enhancing fleet reliability and developing more effective approaches to maintaining vehicles subjected to extreme environmental and operational demands.
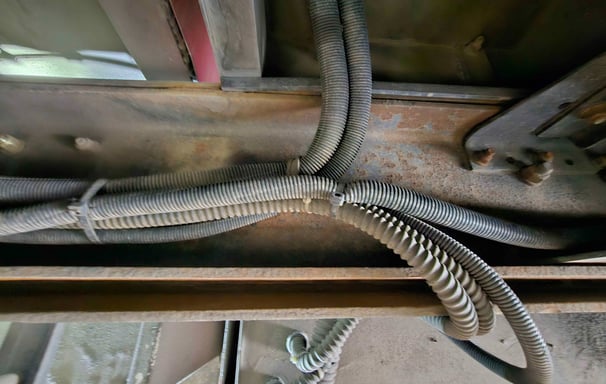
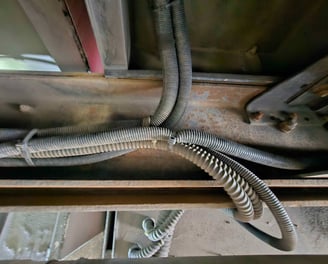